Facilities
Measure what is measurable, and make measurable what is not so.
– Galileo Galilei –
NER AutoLab 1500
This is the work-horse of the RDL a multipurpose triaxial apparatus that can reach 200 MPa confining pressure and 125 deg C. We use this machine to measure ultrasonic velocities, permeability, and other physical properties of rocks. The apparatus can be equipped with various instruments including high pressure syringe pumps to control the pore pressure.
![]() NER autolab 1500. Omar Alamoudi is analyzing ultrasonic wavelets. |
![]() Carolyn Bland is preparing the apparatus to measure the permeability of New Zealand rocks. |
Over the years, the members of the RDL have developed some equipment that works with the AutoLab pressure vessel. Carolyn developed a transient pressure helium permeameter, Nicola has developed endcaps with ultrasonic transducers and fluid injection ports, Ken developed a Low-Frequency Module (LFM see below) to measure the attenuation and dispersion of seismic waves (f~0.01-100 Hz).
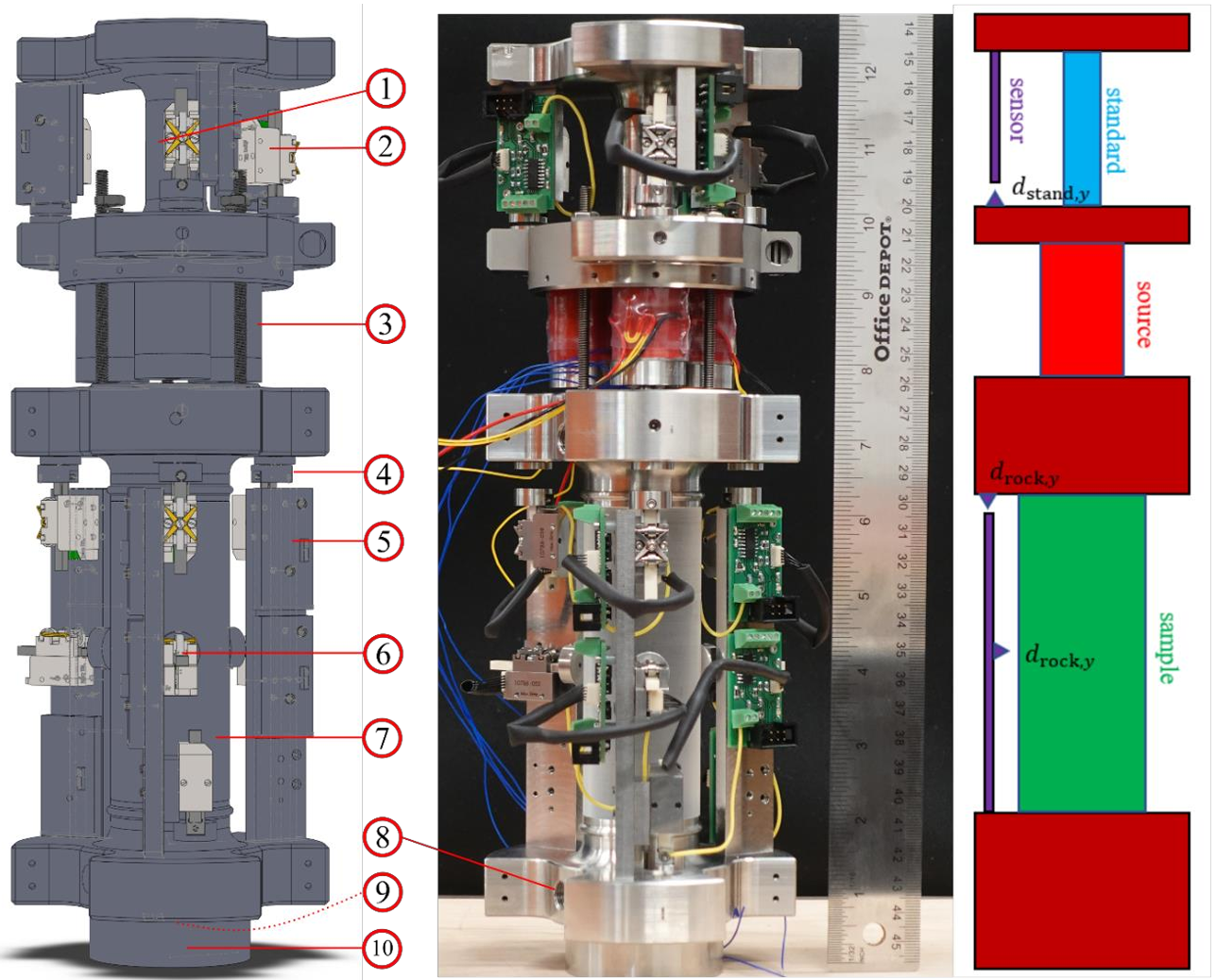
A schematic diagram of the LFM (left) along with the cross-section of the module (middle) and the simplified diagram indicating four main components (right). The number labels are: 1) standard titanium part, 2) piezo LEGS® Linear 6N and capacitive sensors [vertical standard], 3) PICA™ (Power Dynamics Piezo Actuators) actuator, 4) piezo LEGS® Linear 6N and capacitive sensors [vertical sample], 5) PCB boards, 6) piezo LEGS® Linear 6N and capacitive sensors [horizontal sample], 7) rock sample, 8) fluid inlet channel, 9) piezoelectric crystal chamber, and 10) spacer.
Bevo-Q apparatus – seismic wave attenuation in liquids
Bevo-Q resembles the mascot of UT Austin – Bevo the longhorn, and it is an apparatus used to measure the attenuation of seismic waves in liquids. Such an instrument was developed in-house and can measure attenuation at frequencies between 0.01 and 10 Hz.
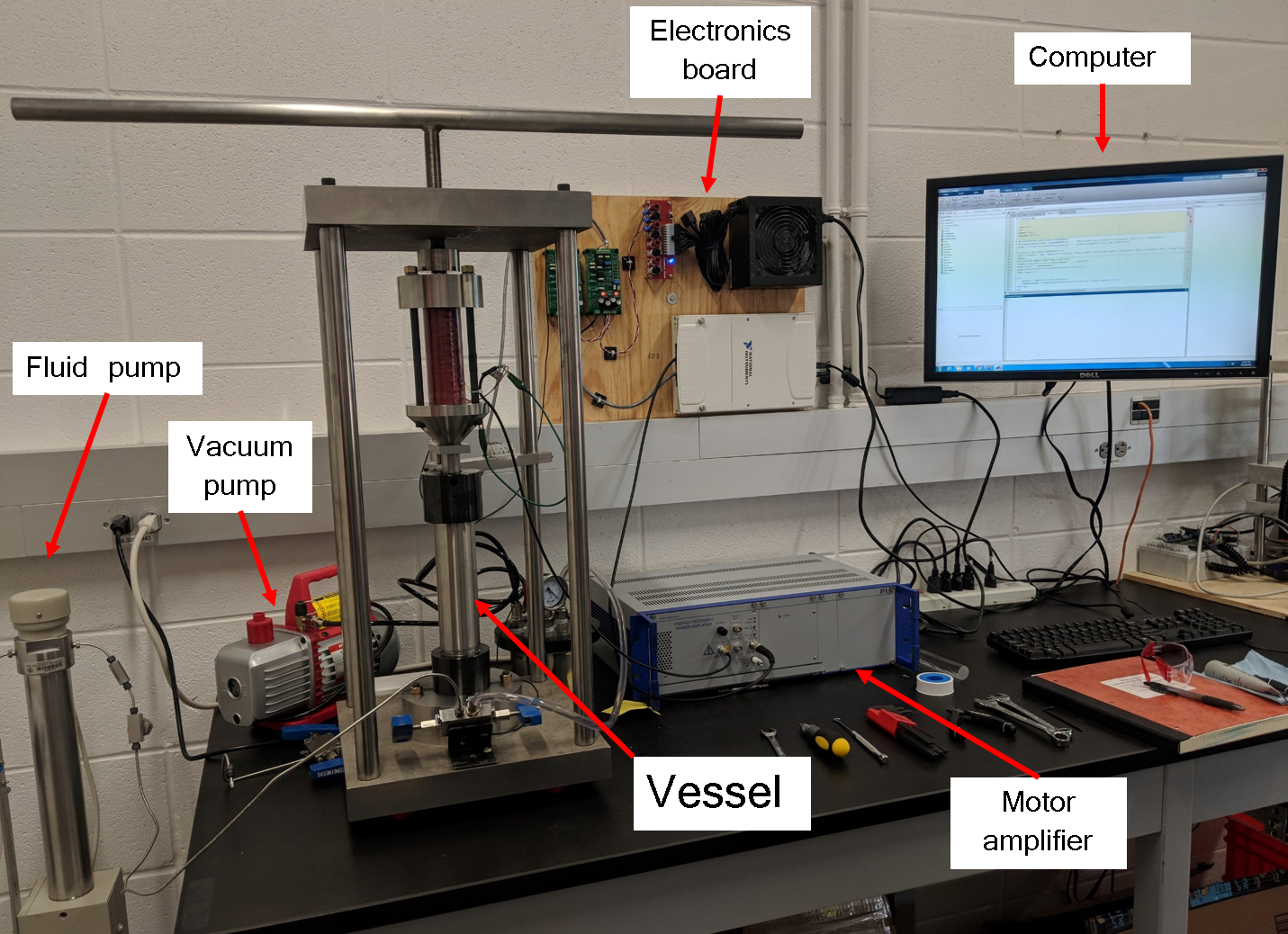
Bevo-Q
Selected references:
- McCann, M.*, Tisato, N., & Spikes, K. (2019) Low-frequency attenuation measurements of fluids. In SEG Technical Program Expanded Abstracts 2019 (pp. 3598–3602). San Antonio, Texas: Society of Exploration Geophysicists. DOI: 10.1190/segam2019-3193361.1
WIGED apparatus – seismic wave attenuation in bubbly liquids
To study the attenuation in bubbly liquids and the Wave-Induced-Gas-Exsolution-Dissolution (WIGED) attenuation mechanism, we built a dedicated instrument that records the deformation of a gas bubble in a liquid undergoing a variation of pressure. The WIGED mechanism causes attenuation of seismic wave because part of the seismic energy is used to dissolve and exsolve the gas in and out of the bubble.
![]() WIGED apparatus |
![]() Images of a CO2 gas bubble undergoing deformation due to a fluid pressure variation recorded with the WIGED apparatus. Bubble deformating a a consequence of a pressure step recorded with the WIGED apparatus. The Bubble rim is highlighted by the blue line and red dots. |
Selected references:
- Jin, Z.*, & Tisato, N. (2020) Measurements of Seismic Wave Attenuation in Bubbly Liquids: Wiged Mechanism, 2020, H015-08. Presented at the AGU Fall Meeting Abstracts.
Energy Controlled Rotary Shear (ECoR)
The ECoR is a rotary shear apparatus that takes advantage of a clock spring to impose a shear stress boundary condition on a couple of cylindrical samples. The apparatus accumulates elastic energy in the clock spring until slip initiates, translating the elastic energy into displacement.
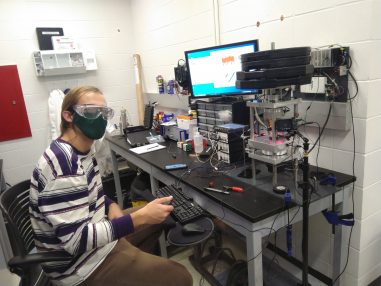
The ECoR instrument and Ethan Conrad preparing to perform an experiment.
Selected references:
- Conrad, E. M.*, Tisato, N., Carpenter, B. M., & Di Toro, G. (2023) Influence of Frictional Melt on the Seismic Cycle: Insights From Experiments on Rock Analog Material. Journal of Geophysical Research: Solid Earth, 128, (19 pages). DOI: 10.1029/2022JB025695
Carbon Dioxide (CO2) and Geothermal Vessel
This pressure vessel allows injecting fluids into a 2.54 cm diameter ~5 cm long cylindrical sample (e.g., carbonated water in ultramafic rocks). The sample holders comprise endcaps with fluid injection ports and embedded piezoelectric transducers that allow for continuous monitoring of acoustic emissions and measurements of ultrasonic velocities. A high-pressure syringe pump controls the confining pressure and measures the deformation of the sample. The sample is jacketed to isolate confining and pore fluid pressures. A second high-pressure syringe pump injects the fluid in the core plug. We can measure the pore fluid pressure, flow rate, acoustic emissions, and ultrasonic velocities to estimate changes in permeability and elastic properties. For example, we can monitor the reaction-induced cracking in ultramafic rocks injected with carbonated water. The system also has two high-pressure syringes to sample the inlet and outlet fluids for analysis throughout the experiment (e.g., dissolved gas volume and compound concentration).
![]() CO2 and Geothermal vessel. Max temperature 350 degree C, max pressure 55 MPa. |
![]() One-inch core plug sample of ultramafic rock covered by a teflon jacket between two sample holders equipped with fluid ports to inject fluids and ultrasonic transducers to measure elastic properties. |
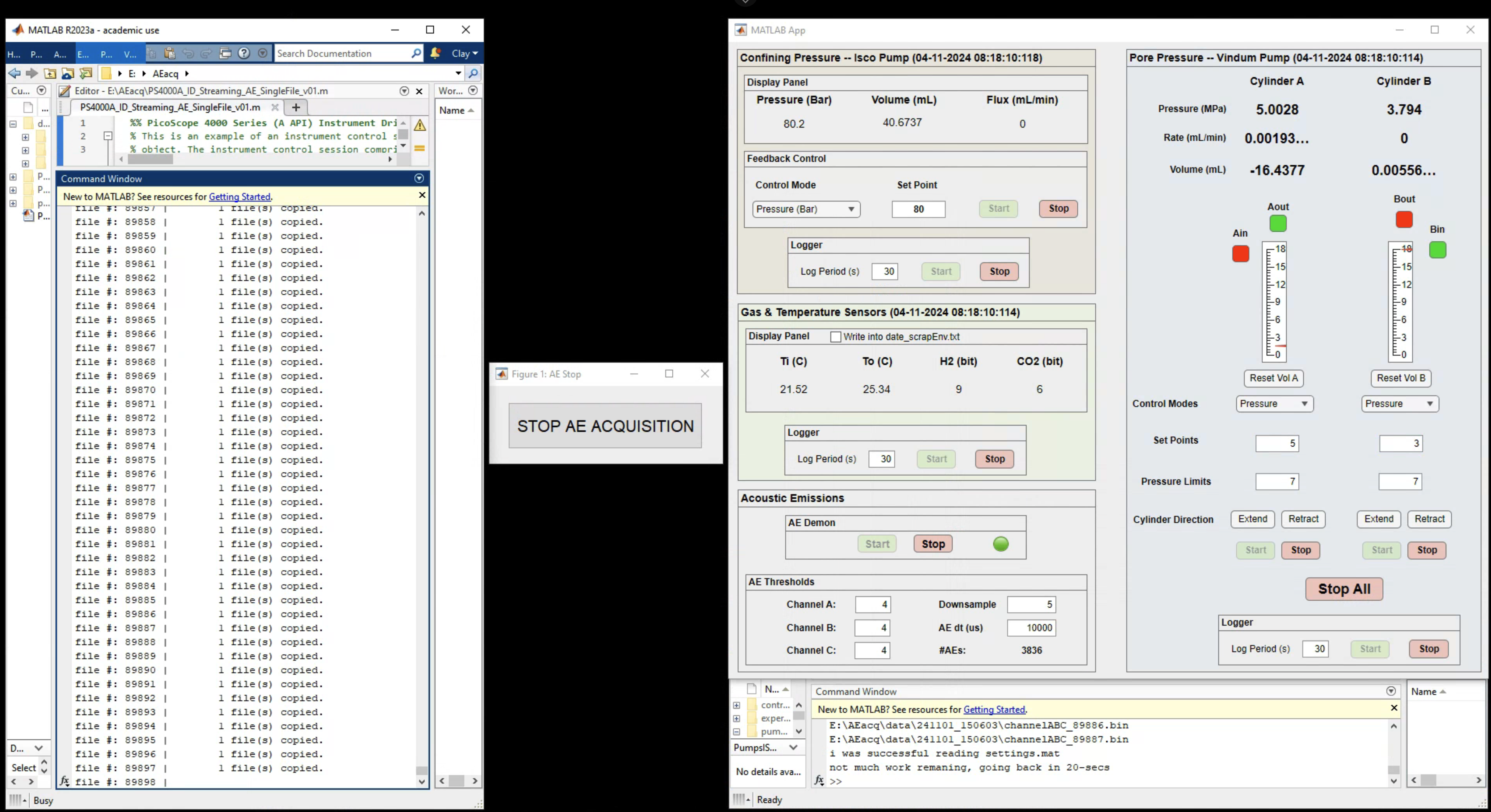
MATLAB software to operate the CO2/geothermal vessel.
Selected references:
- Enhancing fracture permeability due to in situ mineral carbonation: an experimental investigation into reaction-driven cracking in ultramafic rocks, Clay Wood, Nicola Tisato, Nicolas Espinoza and Estibalitz Ukar, AGU 2024 Fall meeting.
X-ray transparent CO2 pressure vessel – in collaboration with the UTCT
This pressure vessel allows injecting fluids into a 1.27 cm diameter ~3 cm long cylindrical sample (e.g., carbonated water in ultramafic rocks) while CT-scanning the sample to obtain in-situ observations of mineral dissolution/precipitation. The sample is jacketed to isolate confining and pore fluids and placed between two endcaps that have fluid injection ports and pressure sensors that, along with a syringe pump that imposes a precise flow rate, allow permeability measurements. A high-pressure nitrogen cylinder with a pressure regulator controls the confining pressure. This apparatus, similar to the Carbon Dioxide and Geothermal Vessel, permits monitoring the reaction-induced cracking in ultramafic rocks injected with carbonated water. The system is also equipped with a vacuum pump and a gas trap to analyze the gases after extraction from the sample (e.g., to monitor hydrogen production).
![]() The X-ray transparent CO2 pressure vessel apparatus and the sample assembly. |
![]() The piece of software (written in Python and running in a RaspBerry PI) to control the X-ray transparent CO2 pressure vessel. |
![]() Top view of the X-ray transparent CO2 pressure vessel apparatus. |
![]() Front view of the X-ray transparent CO2 pressure vessel apparatus. |
Selected references:
- Evaluating the Impact of CO2 Mineralization on the Elastic Properties of Ultramafic Rocks, S. Almeshari, N. Tisato, C. Wood, IMAGE 2024 meeting.
X-RETTA – combining Rock-physics with X-ray imaging – in collaboration with the UTCT
The X-Ray Transparent Tri-axial Apparatus (X-RETTA) allows us to load cylindrical rock samples triaxially while simultaneously embedding them inside Micro-scale X-ray Computed Tomography (microCT) scanners as shown in the images below. This is possible due to the small footprint of the device and the use of flexible hydraulic tubing that is used to control the hydraulic fluid pressures of different X-RETTA chambers. Given a cylindrical rock sample with a diameter of 25mm (~1 inch), the X-RETTA is capable of producing an axial load of ~160MPa, and confining pressure of about ~ 21MPa. Also, the X-RETTA allows for accessing the sample pore pressure. This allows for either drained or undrained experimental configurations. Finally, we built a custom permeameter that integrates with the X-RETTA to measure the permeability of the sample while the apparatus is mounted inside the microCT scanner at UTCT.
![]() Omar Alamoudi with the X-RETTA is ready to perform an experiment. |
![]() The triaxial cell of the X-RETTA mounted inside the CT-scanner of the UTCT lab. |
Selected references:
- Alamoudi, O.*, and Tisato, N., (2023): Permeability and fracture evolution with confining pressure: an experimental study utilizing X-ray computed tomography and pulse-decay permeability measurements. Tomography for Scientific Advancement – North America (ToScANA) – Austin.
Ultrasonic facility
The RDL equipment includes i) a 4 channels 100 MHz sampling rate digital oscilloscope, ii) a 10 MHz 8 channels 12 bits oscilloscope for acoustic emission (AE) recording, iii) a 100 MHz 4 channels 16 bits oscilloscope, iv) two 20 MHz function generators, v) 3 pulse generators for ultrasonic transducers, vi) 9 Olympus ultrasonic transduces for measurements of Vp and Vs in samples with diameters greater or equal 1/2 inches, vii) a set of 5 acoustic emissions (AE) preamplifiers and sensors, and vii) two high precision (5.5 and 6.5 digits) multimeters.

The ultrasonic facility at the RDL
Analytical instruments and computational facilities
The RDL has i) a helium pycnometer to measure sample porosity, ii) a BET surface area analyzer (autosorb), iii) a falling-head permeameter.
Several Linux workstations with multiple cores, GPUs, and up to 256 GB of memory and the Texas Advanced Computing Center (TACC).
Rock preparation lab
To prepare our experiments and core plugs, the RDL has a dedicated room, that accommodates a fume hood, a lathe with surface grinder, a milling machine, two drill presses and other tools.
![]() RDL laboratory. Omar Alamoudi is preparing his experiment. |
![]() Carolyn Bland is preparing a core plug from a cobble collected in New Zealand. |